Common faults after installing hydraulic breaker on excavator
1. Working principle of hydraulic system of excavator equipped with breaker
For excavators equipped with hydraulic breaker, other working devices of the excavator can still work normally regardless of whether the breaker works or not.
The main reversing valve of this system generally adopts the spare valve reserved on the main working valve group of the excavator. The pressure oil for the breaker is provided by a main pump of the excavator. The working pressure of the breaker is adjusted by installing a relief valve; a high-pressure stop valve must be installed at the inlet and outlet of the breaker to facilitate the adjustment and maintenance of the working system parameters.
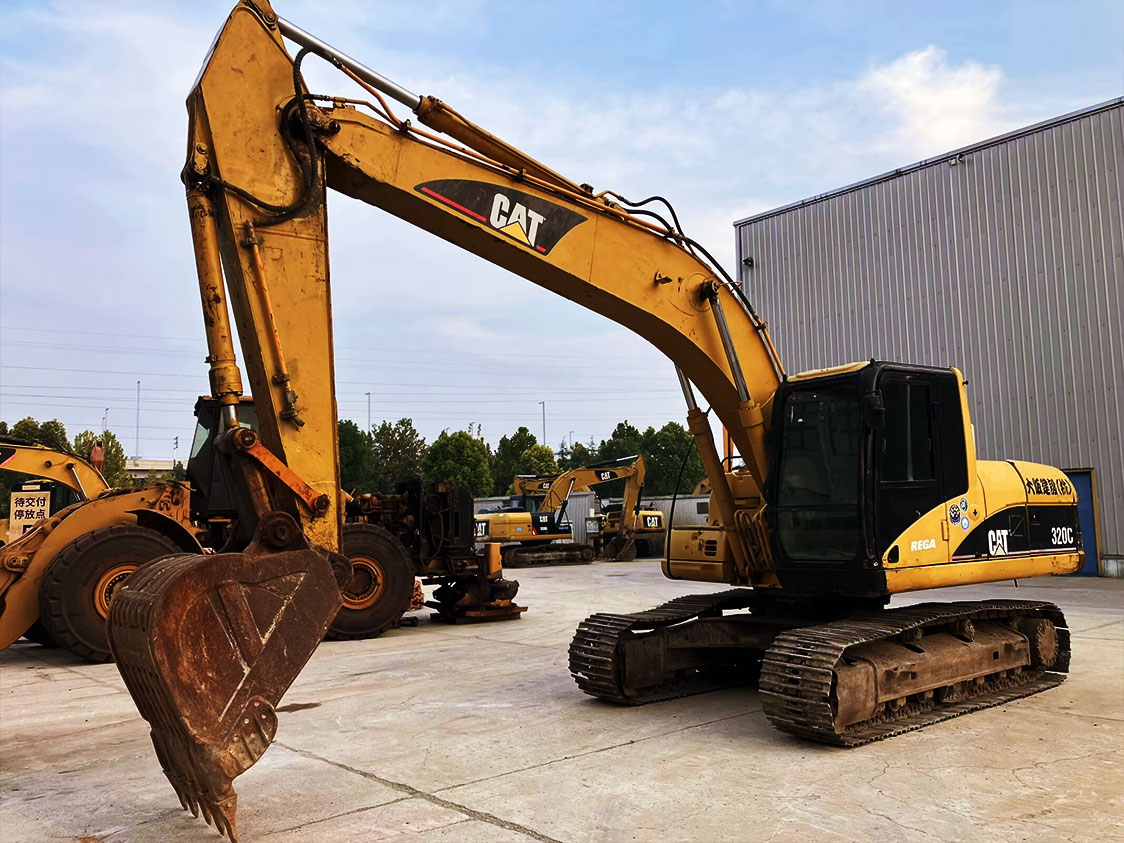
2. Common faults
Operational errors, nitrogen leakage of the breaker, improper maintenance and other phenomena will cause wear of the working valve of the breaker, bursting of the pipeline, local overheating of the hydraulic oil and other faults. The reasons are, first, unreasonable technical configuration and second, improper on-site management.
The working pressure of the breaker is generally 20MPa and the flow rate is about 170L/min, while the system pressure of the excavator is generally 30MPa and the flow rate of the single main pump is 250L/min. Therefore, the relief valve needs to undertake heavy diversion and unloading work. Once the overflow valve is damaged but not easily detected, the breaker works under ultra-high pressure. First, the pipeline bursts and the hydraulic oil is partially overheated. Then the main reversing valve is seriously worn and the hydraulic circuit controlled by other valve cores of the main working valve group of the excavator (the next valve core pointed to by the main oil circuit when in the middle position) is contaminated; and because the return oil of the breaker generally does not pass through the cooler but directly returns to the oil tank through the oil filter, such a circulating oil circuit may cause the oil temperature of the working oil circuit to be high or even too high, seriously affecting the service life of the hydraulic components (especially the seals).
3. Troubleshooting measures
The most effective way to prevent the above faults is to improve the hydraulic circuit. First, add an overload valve to the main reversing valve (the same type of overload valve as that of the boom or bucket working valve can be selected). Its set pressure should be 2~3MPa higher than the overflow valve, which can effectively reduce the impact of the system and ensure that the system pressure is not too high when the overflow valve is damaged; second, connect the return oil pipeline of the working oil circuit to the cooler to ensure timely cooling of the working return oil; third, when the main pump flow exceeds 2 times the maximum flow of the breaker, install a diverter valve in front of the main reversing valve to reduce the load of the overflow valve and prevent overheating caused by a large amount of oil supply through the overflow valve.
1 Brief analysis of energy loss of single-bucket hydraulic excavator during operation
In addition to general mechanical loss, pipeline loss and pump efficiency loss, the energy loss of single-bucket hydraulic excavator during operation also includes the following main aspects:
(1) Inefficiency caused by incorrect engine injection advance angle
(2) Energy loss caused by mismatch between engine and hydraulic pump, that is, when the engine and hydraulic pump work together, there is a joint working characteristic, in which the joint working efficiency is related to the speed, pressure and flow of the pump. In general, the engine-hydraulic pump system is unlikely to be in the best economic working state under various working conditions, resulting in a certain amount of energy loss. The total power loss of the engine-hydraulic pump is:
Nz=P0Qmax/ηmηy
Where: ηm——engine mechanical efficiency, that is, ηm=Ne/Nt (N-engine effective power; N-engine indicated power);
ηy——total efficiency of the hydraulic pump. It should be noted that the efficiency ηm and ηy of the engine and hydraulic pump at low load and high speed are very low.
(3) Hydraulic oil flow loss, the power loss caused by flow loss ΔN=PΔQ (P is the hydraulic oil pressure, ΔQ is the lost flow), consists of the following parts:
(a) Losses caused by hydraulic system leakage.
(b) When each control valve is in the middle position (excavator is not working), if the engine speed is not reduced, the loss of hydraulic power is:
Ny1=P0Qmax
Where: P0——back pressure of hydraulic system; Qmax——maximum flow of hydraulic pump.
(c) Overflow loss, the power loss of hydraulic oil caused by overflow is:
Ny2=PmaxΔQ
Where: Pmax——opening pressure of overflow valve (approximately equal to the maximum pressure of the system); ΔQ——overflow volume.
The total power loss of engine-hydraulic pump system caused by overflow is:
Nz=Ny2ηm/ηy=PmaxΔQ/ηmηy
ηm\ and ηy under this working condition are relatively high.
(4) The pressure loss of hydraulic oil is mainly composed of two parts: the first part is the loss along the way when hydraulic oil passes through pipes and joints, etc., which is unavoidable; the other part is the loss caused by throttling of hydraulic oil through control valve when the excavator performs fine work.
2 Control system scheme and function
This control system is mainly aimed at energy saving. However, it is impossible to completely eliminate the above energy loss without changing the internal structure of the hydraulic system and the engine. Based on the principle of being active, prudent and practical, the developed control system is determined to use the hydraulic system pressure as a judgment signal to judge the working state of the excavator. According to the different states of the excavator, the microcomputer controls the engine throttle through the stepper motor to stabilize the engine near the required speed. The principle is shown in Figure 1.
This control system has the following functions:
2.1 Automatic idling
When the excavator is not working, the computer automatically reduces the engine throttle opening to make the engine idle. The judgment is based on the hydraulic system pressure. According to actual measurements, when all control valves are in the middle position, the system pressure is about 5MPa, and when the excavator is working, the system pressure is above 1MPa, so the judgment pressure is set at 2MPa. In order to ensure that the excavator is indeed not working, the system is required to start operating the throttle after maintaining a pressure of less than 2MPa for 4s. When the system pressure is higher than 2MPa, the excavator is considered to be in working condition, and the computer immediately controls the engine to quickly restore it to the set working speed.
2.2 Power mode control
The system is equipped with three gears: high, medium and low, and the corresponding engine speeds are 2000r/min (i.e. the highest speed), 1760r/min (85% of the highest speed) and 1300r/min (65% of the highest speed). When the driver selects a gear according to work needs, the computer can control the engine to work stably near the corresponding speed. Since the absorption torque of the full-power variable pump is constant in the constant power adjustment section, the engine power of the high, medium and low gears is also 11%, 85% and 65% of the full power respectively.
2.3 Overload function when overloaded
The maximum pressure set by the hydraulic system of the excavator has a certain margin. When the system is overloaded for a short time, it generally does not have much impact on the system, but it cannot be overloaded for a long time, otherwise it may affect the life of the system and other components and produce other adverse consequences. To this end, the control system is equipped with a short-term overload function. When the hydraulic system pressure exceeds the original design maximum pressure (tentatively set at 30MPa) within ZMPa, the excavator can still work normally for 8s, so that the working device can overcome the temporary large resistance to improve work efficiency. At the same time, in order to protect the safety of the system and prevent the hydraulic system from overloading for a long time, after 8s of overload, the control system automatically reduces the engine speed to about 1100r/min and alarms, allowing the driver to change the operation mode. When the system pressure drops below the maximum design pressure, the control system quickly restores the engine to the original speed.
2.4 Overflow control
When the hydraulic system pressure approaches or reaches the overflow valve opening pressure (tentatively set at 32MPa), the control system automatically and quickly reduces the engine speed to 1100r/min to reduce the overflow volume; when the hydraulic system pressure is less than the set maximum pressure (tentatively set at 30MPa), the control system will quickly restore the engine to the original speed.
2.5 It has the functions of manual control and microcomputer automatic control in parallel, and manual control priority
3 Energy-saving effect of the control system
3.1 Reducing the mid-position loss of the hydraulic system
When the single-bucket hydraulic excavator is temporarily in an inoperative state and all the control valves are in the middle position, the pressure of the hydraulic system is generally low. According to the variable pump characteristics, the flow rate reaches the maximum at this time, which is Qmax shown in Figure 2. The total power loss of the system is:
N1=(QmaxP0/ηeηB)+Nf (1)
Where: P0——back pressure of the hydraulic system; ηe——effective efficiency of the engine; ηB——hydraulic pump efficiency; Nf——additional power.
The value of QmaxP0 is the area enclosed by P0-C-Qmax-0 in Figure 2.
The automatic idle function of the automatic control system can realize the automatic and rapid reduction of the engine throttle when each control valve is in the middle position, so that the engine works at the specified minimum speed. At this speed, the working characteristic curve of the hydraulic pump is the Pmax-a-b-c-Q0 curve in Figure 2. In the figure, the value of Q0 is basically proportional to the speed of the hydraulic pump, and the size of the additional power Nf is also approximately proportional to the speed. When the engine speed drops from ne to ne', its energy consumption decrease rate is approximately:
un=(ne-ne?)/ne (2)
For example, for the DF-WY32 single-bucket hydraulic excavator produced by YTO, ne=2000r/min, according to the idle speed characteristics of the engine, ne?=800r/min is determined, and the energy consumption decreases by about 60%. After the speed drops, the energy consumption decrease of the variable pump part is the shaded area in Figure 2.
3.2 Economic matching operation of the engine and variable pump
The combined working efficiency of the engine and the variable pump is:
η=ηeηB=MeneP0Q0/GehnMInI=f(Me, ne, MI, nI) (3)
The combined working efficiency η of the system is only a function of the pressure P0 and the speed nI (or ne). Since the pressure depends on the external load, only the speed ne is selectable. For a certain engine-variable pump system, for each pressure P0, there is an optimal speed ne1 that maximizes the combined working efficiency η. For the DF-WY32 single-bucket hydraulic excavator, the optimal speed of the engine is around 1700r/min at different working pressures. For this reason, the automatic control system is equipped with the most economical working gear (i.e., the middle gear in the power mode control). When this gear is selected, it can save about 13% of energy compared to working at the rated speed (2000r/ndn).
3.3 Reduce throttling loss
Throttling loss mainly occurs in light load and low speed operation. As shown in Figure 3, the required working pressure of the working device is Pl, and the required working flow is Q2, but on the variable pump external characteristic curve AB, Pl and Q2 correspond to the two working points d and c respectively. To meet the needs of work, the driver must use the partial throttling effect of the control valve to increase the working pressure of the variable pump to P2 so that it works at point c. The resulting throttling loss is: δ=Nj(P2-P1)Q0. , which is the area of the shaded part in Figure 3. If the speed of the variable pump can be changed so that the working characteristic curve passes through point e, this loss can be eliminated. The working mode control of this control system is mainly set for this purpose. Properly selecting one of the working gears will not make the working curve pass through point e, but it can be close to point e, thereby reducing throttling losses.
3.4 Reduce overflow loss
Overflow loss mainly occurs at low speed and overload. As shown in Figure 4, when the flow rate required by the working device is Q1, which is less than Q0, or the working pressure exceeds the set pressure of the overflow valve, the overflow valve will be opened, resulting in overflow loss. The lost energy is now (Q1-Q0)
Pmax, whose value is the shaded area in Figure 4. In order to eliminate or reduce overflow loss, the automatic control device can automatically reduce the engine speed before the overflow alarm is turned on, so that the original working characteristic curve AB becomes ah, until the engine drops to the set minimum speed. Even if the overflow cannot be completely eliminated, the overflow volume has been reduced a lot.
4 Function
The main purpose of this system is energy saving, while also improving operating performance, reducing the driver's labor intensity and improving operating efficiency.
4.1 Energy saving effect
The system can effectively reduce the median loss, overflow loss and throttling loss of the excavator. The system is installed on DF-WY32, and experience has shown that it saves about 10% to 15% of energy. For single-bucket hydraulic excavators with single pump and fixed-displacement pump systems, the effect is better.
4.2 Improve operating performance
After adopting this control system, once the driver determines the power mode of the system according to the operating object, the engine can be controlled by the computer regardless of the working state of the excavator, and it can be in a more ideal working state, thereby improving the operating performance.
4.3 Improve operating efficiency
The short-term overload function of this control system not only effectively protects the safety of the system, but also improves the excavator's ability to overcome short-term overload, thereby saving time and improving efficiency. In addition, after the pressure oil energy loss of the hydraulic system is reduced, the heat generation of the hydraulic system is reduced, thereby improving and stabilizing the working performance of the system.